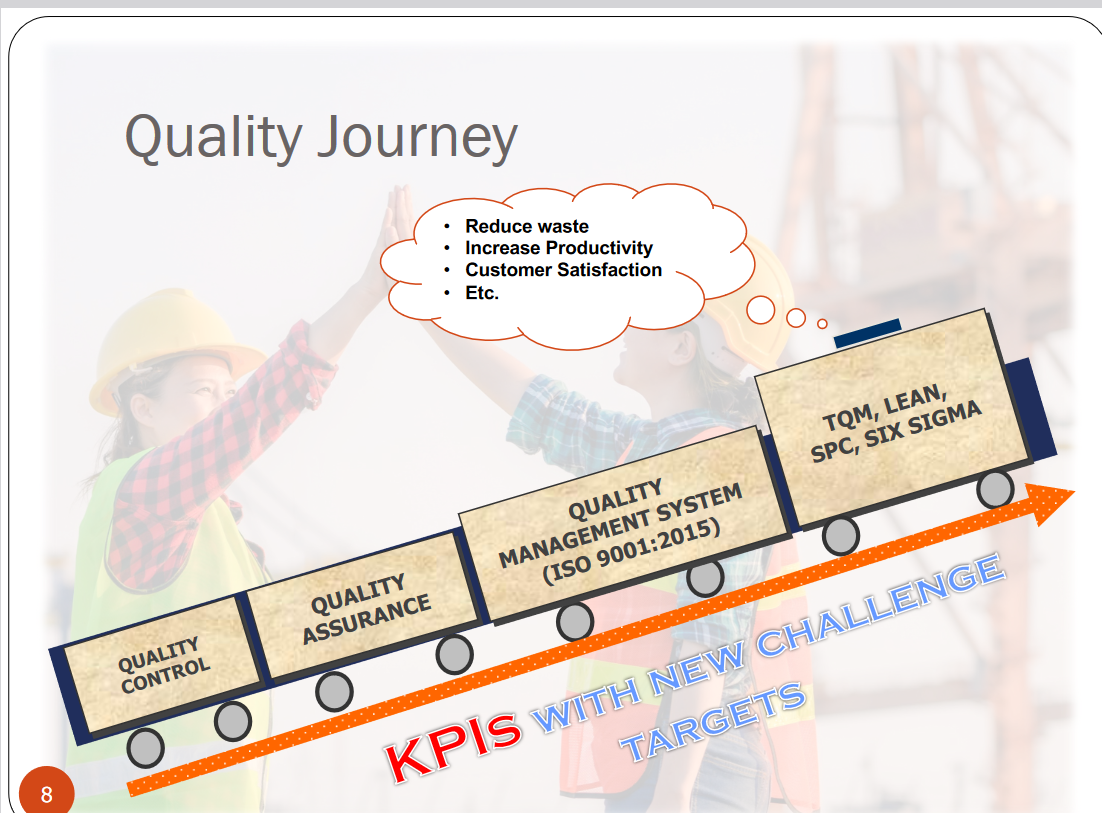
What is Quality Management in Construction?
Quality management in construction is a systematic approach to ensuring that construction projects meet established standards, specifications, and client requirements with a focus on delivering high-quality outcomes. It encompasses a range of processes, practices, and principles aimed at preventing defects, improving efficiency, and achieving customer satisfaction. Quality management in construction is vital to ensure that structures are safe, durable, and meet performance expectations. Here are key components of quality management in the construction industry.
- Quality Planning: Quality management starts with developing a quality plan. This plan outlines the project’s quality objectives, standards, and specifications. It also identifies the roles and responsibilities of various stakeholders, the quality control processes to be used, and the testing and inspection requirements.
- Quality Control (QC): QC involves monitoring and inspecting construction activities and outputs to ensure that they comply with established standards and specifications. This includes on-site inspections, material testing, and documentation of results. Any non-conformities or deficiencies identified during QC should be addressed promptly.
- Quality Assurance (QA): QA encompasses the systematic processes and procedures designed to prevent quality issues from occurring in the first place. This includes creating and implementing best practices, training workers, and continuously improving processes to enhance overall quality. QA is a proactive approach to quality management.
- Quality Inspections: Regular inspections are a key part of quality management. Inspectors assess the work at various stages of the construction process to verify compliance with design and performance requirements. Inspections may be conducted by internal quality control teams or external third-party inspectors.
- Documentation: Accurate and detailed documentation is crucial for quality management. This includes maintaining records of all quality-related activities, such as test results, inspection reports, and any corrective actions taken. Documentation helps in tracking progress and demonstrating compliance.
- Continuous Improvement: Quality management involves a commitment to continuous improvement. It includes analyzing data, identifying areas for improvement, and implementing corrective and preventive actions to enhance overall quality. This cycle of improvement ensures that lessons learned from one project are applied to future projects.
- Risk Management: Identifying and managing risks is an important aspect of quality management. Understanding potential quality-related risks and taking proactive steps to mitigate them helps prevent issues from arising during construction.
- Client Communication: Effective communication with the client is essential for quality management. Ensuring that the client’s expectations are clearly understood and met is a key component of achieving satisfaction. This includes regular updates on project progress and addressing any concerns or changes in requirements.
- Supplier and Subcontractor Management: Quality management extends to the suppliers and subcontractors involved in the project. Ensuring that these entities meet quality standards and adhere to agreed-upon specifications is crucial for overall project quality.
- Quality Standards and Regulations: Compliance with relevant industry standards, building codes, and regulations is fundamental to quality management. Staying up-to-date with the latest standards and ensuring that the project aligns with them is vital.
- Audits and Reviews: Periodic audits and reviews of the quality management system can help identify areas for improvement and assess the overall effectiveness of the quality control and assurance processes.
Effective quality management in construction ultimately leads to improved project outcomes, reduced rework, enhanced safety, and increased client satisfaction. It is an ongoing process that requires a commitment to excellence and a collaborative effort among all project stakeholders.
ISO 9000 in Construction
ISO 9000 is a series of international standards for quality management systems that can be applied to various industries, including the construction sector. The ISO 9000 standards are designed to help organizations establish and maintain effective quality management systems to enhance the quality of their products and services. In the context of the construction industry, ISO 9000 standards can be used to improve the quality of construction projects and processes. Here’s a brief overview of ISO 9000 in construction:
- ISO 9000 Series: The ISO 9000 series consists of several standards, with ISO 9001 being the most well-known and widely used. ISO 9001 sets the criteria for a quality management system and provides a framework for organizations to establish, implement, maintain, and continually improve their quality management processes.
- Applicability to Construction: ISO 9001 and other ISO 9000 standards can be applied to construction companies, contractors, engineering firms, and other organizations involved in construction projects. These standards help construction firms ensure that their processes, project management, and quality control meet international best practices.
- Key Principles: ISO 9001 is based on several key principles that are particularly relevant to the construction industry, including customer focus, leadership, engagement of people, process approach, continuous improvement, evidence-based decision-making, and relationship management.
- Benefits in Construction: Implementing ISO 9000 standards in construction can offer several benefits, including:
- Enhanced Quality: ISO 9000 standards help organizations establish robust quality control and assurance processes, leading to improved construction quality.
- Improved Efficiency: Standardizing processes and documentation can lead to increased efficiency and reduced errors or rework.
- Reduced Risk: A well-implemented quality management system can help identify and mitigate risks, leading to more successful construction projects.
- Client Satisfaction: Meeting ISO 9001 standards can help enhance client satisfaction by demonstrating a commitment to quality and customer-focused processes.
- Legal and Regulatory Compliance: ISO 9000 standards can assist construction companies in meeting legal and regulatory requirements related to quality and safety.
- Certification: Organizations in the construction industry can seek ISO 9001 certification, which is provided by accredited certification bodies. ISO 9001 certification is a third-party verification that the organization’s quality management system meets the requirements of the standard.
- Integration with Other Standards: ISO 9000 standards can be integrated with other relevant standards in the construction industry, such as ISO 14001 for environmental management and ISO 45001 for occupational health and safety management, to create a comprehensive management system that addresses quality, safety, and environmental concerns.
Implementing ISO 9000 standards in construction requires a commitment to the principles of quality management and a dedication to ongoing improvement. While it may involve an initial investment of time and resources, the long-term benefits, including improved project outcomes, client satisfaction, and compliance with industry standards, make it a valuable framework for construction organizations seeking to enhance their quality management processes.
In conclusion, quality management in the construction industry is a fundamental process that ensures construction projects meet or exceed established standards and client expectations. It encompasses a range of practices, from quality planning and control to continuous improvement and adherence to regulations. Effective quality management leads to safer, more efficient, and more durable structures, while also enhancing client satisfaction. Organizations that implement robust quality management systems, including ISO 9000 standards, demonstrate a commitment to excellence and are better equipped to succeed in the competitive and demanding construction sector.